Possible problems and the Lanat solution
The Lanat solution
The following illustrations demonstrate how Lanat repairs and withstands damage caused to concrete by chemicals, fork-lift trucks and other vehicles, as well as other physical strain.
Today’s warehousing methods, which utilizie both manual and automatic guided vehicle systems, require sealed, even flooring, while operators of manual driven fork-lift trucks, reduce the risk of back and leg injuries when joints, cracks and holes are repaired.
Worn concrete causes cracks that are not completely open.
Problem
Worn concrete causes cracks that are not completely open.

Worn concrete causes cracks that are completely open.
Problem
Worn concrete causes cracks that are completely open.
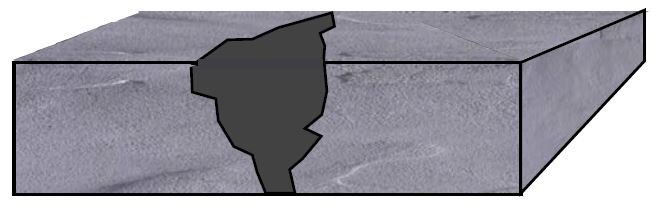
Water flows away from the drain rather than towards it.
Problem
Water flows away from the drain rather than towards it.

Uneven levels – less than 3 cm
Problem
Uneven levels – less than 3 cm

Worn truck paths.
Problem
Worn truck paths.

Damaged transport grooves for acidic or alkaline aqueous solutions.
Problem
Damaged transport grooves for acidic or alkaline aqueous solutions.

The Lanat solution
Base: Lanat Resistent
Supplement: = Lanat Spackel
Supplement: = Lanat Nivelleringsmassa
Top: Lanat Resistent
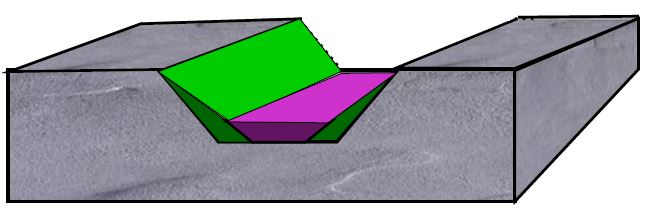
Plastic-coated drying room floor (20-80°C) on which cracks have occured because the plastic is either too hard or too soft.
Problem
Plastic-coated drying room floor (20-80°C) on which cracks have occured because the plastic is either too hard or too soft.

Repair above sunken wires.
Problem
Repair above sunken wires.

Scaling against a wall.
Problem
Scaling against a wall.

Leakage into the concrete from, for example, a fan room. The fan cabinets are so low that there is no room to repair the damage by any other method.
Problem
Leakage into the concrete from, for example, a fan room. The fan cabinets are so low that there is no room to repair the damage by any other method.

The Lanat solution
Base: Lanat Resistent
Supplement: = Lanat Nivelleringsmassa
Pour Lanat Nivelleringsmassa from the side. Since it penetrates into concrete, it seals cracks and fissures.
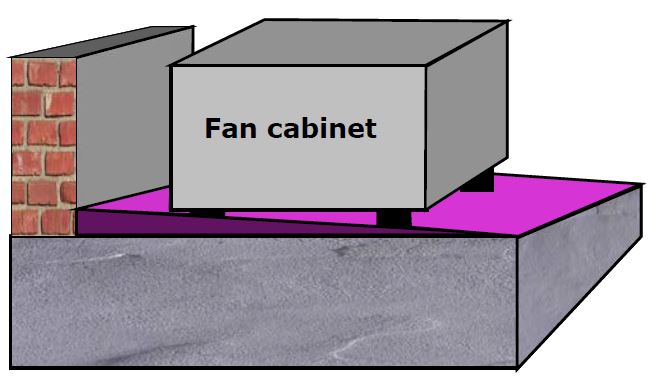
When asphalt tapers horizontally.
Problem
When asphalt tapers horizontally.

Slipery ramps.
Problem
Slipery ramps.

The Lanat solution
Base: Lanat Resistent
=
Alternative 1– Additional Lanat Resistent and anti-skid agent #2
Alternative 2 – Lanat Nivelleringsmassa and a generous amount of silicon sand #2
Top: Lanat Resistent

Surfaces which must endure high-impact stress
Problem
Surfaces which must endure high-impact stress

The Lanat solution
Base: Lanat Resistent
=
Lanat Nivelleringsmassa (45%) complemented with silicon sand #1 (55%).
The sand adds elasticity to the plastic, which acts to cushion against stress.

Applying Lanat to Oily Floors
No matter how well we clean, we can’t get at oil which has seeped deep into a concrete floor. However, experience shows us that the illustrated procedure enable Lanat Plastics to coat, seal and grip – even on oil-damaged concrete.
Cleaning and Preparation
Diamond-sand the floor until at least 90% of the surface is well abraded.
Se figure 2.1 and 2.2.
Before sanding
= Oily patches (from leaking machinery, etc)
Figure 2.2
After sanding
= Well abraded oil patch
Figure 2.2
Marks from the oil-damaged patches remain, but Lanat Resistent will grip the entire surface, and adhere as well as it does do undamaged concrete.
Experience has proven that an application of Lanat Resistent to this well-sanded surface will penetrate oil remaining on the concrete surface and adhere to the rock particles in the concrete.
See figure 2.3 which shows a grain of sand immersed in oil in the upper layer of the concrete.

Figure 2.4 shows that with Lanat Resistent the oil is repulsed and lifts away from the rock particles, leaving the Lanat on the stone surface. Note that the oil is forced above the Lanat lacquer.
The oil membrane diminishes with each application of Lanat, and does not usually cause slipperiness. To prevent this completely, add approximately 5-25 g/m2 of anti-skid agent #2 to the final treatment.

Lanat Resistent is a product well suited to the treatment of concrete floors suffering from oil damage.
However, our forty years of experience with this process convinces us that these results are reached only when the floor has first been diamond sanded.
Applying Lanat to Damp Floors
If the concrete floor to be treated absorbs ground moisture, Lanat Plastics will not retain their characteristic long-lasting adhesion so well. Unfortunately, both dry and wet concrete slabs look identical if the air circulating above them is dry and warm. The upper layer of concrete (floor B, figure 3.1) emits moisture into the the air, wich can lead to a misleading idea of the dryness or dampness of the floor.
One example of this problem is that it is difficult to judge whether a cellar floor can be covered with plastic or not.
Floor A: Thoroughly dry concrete slab
= Shingle
Figure 3.1
Floor B: Concrete slab that looks dry but is very damp inside
= Water
Figure 3.1
If the floor is covered with 2 mm of plastic, the following will be the results (figure 3.2).
Floor A: A good result
= Shingle
Figure 3.2
Floor B: A covering that will be penetrated by water
= vatten
Figure 3.2
The moisture in the layer between plastic and concrete increases in the case of floor B. When this volume exceeds 10%, the plastic constricts as shown in figure 3.2, floor B. The damage to floor B is first indicated by rising bubbles which will eventually cause the plastic to flake off.
To avoid misjudging the dampness of a floor, you are recommended to lay 0.2 mm
diffusionproof plastic wrap over 2 m2 of the floor. After one week any accumulated dampness under the plastc-wrap can be measured using the calcium-carbide method.
If there is a notable increase in the level of dampness, the floor should be treated with a single coat of Lanat Resistent. This simple treatment, wich gives a layer of 40 μm when dried, will protect the concrete from dust, and is easily cleaned and cared for. This treatment allows floor-dampness to pass through the single layer of floor coating, which still remains durable.
Laying several layers of plastic coating on damp floors can result in the type of damage described in figure 3.2. Today’s floors are usually of such high constructional quality that this type of problem rarely occurs, although, one should always be aware of the damage that confined dampness can cause.
In figure 3.3 floor B is covered with one coat of Lanat Resistent (40 μm dry). Dampness can easily permeate it.
= water
= Lanat Resistent (40 µm)
Figure 3.3
If, because of significant corrosion in the outer concrete layer, a concrete floor with a high moisture content must be covered with a Lanat layer thicker than 40 μm, a layer of hard-quality Lanat plastic (app. 15 mm) can be applied.
Although the damp concrete underneath the plastic will have the undesireble effect of diminishing the adhesion of the plastic to the floor, this thicker coating will withstand industustrial traffic for manny years.
= water
= Lanat Nivelleringsmassa (45%) complemented with silicon sand #1 (55%).
Figure 3.4